新材料
来源:未知 日期:2016-12-22 点击:次
《中国制造2025》将新材料作为十大重点领域。《中国制造2025》大力推进新材料产 业发展,力争在2025年以前使我国新材料产业进入世界一流强国行列。报告把特种金属功能材料、高性能结构材料、功能性高分子材科、特种无机非金属材科和先进复合材料为发展重点,积极发展军民共用特种新材料,加快技术双向转移转化,促进新材料产业军民融合发展。
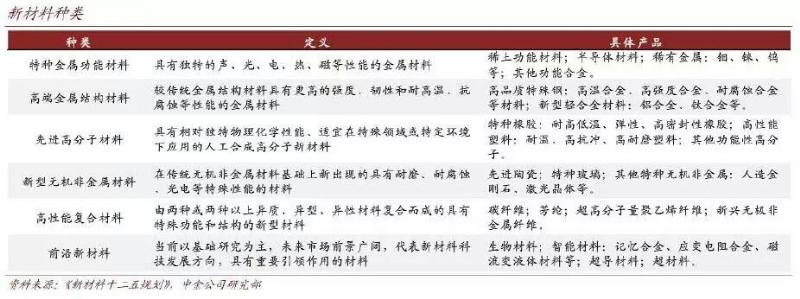
军工新材料是新一代武器装备的基础。军用新材料是新一代武器装备的物质基础,也是当今世界军事领域的关键技术,是现代精良武器装备的关键,是军用高技术的重要组成部分。世界各国对军用新材料技术的发展给予了高度重视,加速发展军用新材料技术是保持军事领先的重要前提。
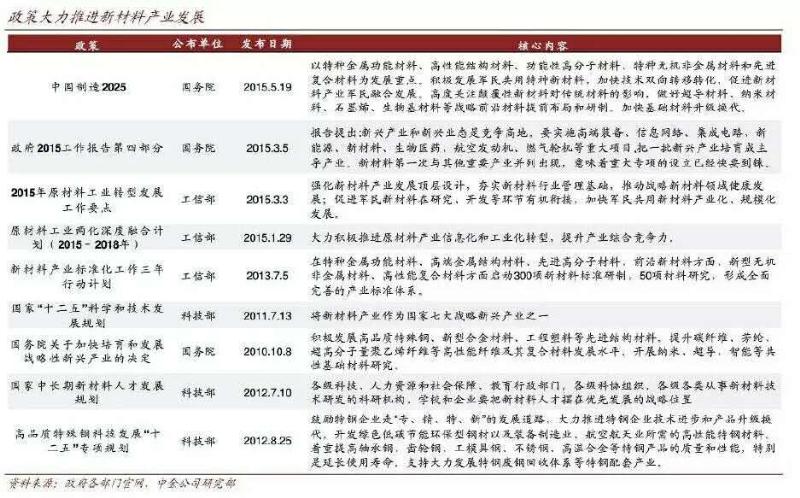
复合材料:先进复合材料具有高比强度、高比模量、耐烧蚀、抗侵蚀、抗核、抗粒子云、透波、吸波、隐抗高速撞击等一系列优点,是国防工业发展中最重要的一类工程材料。大体分为:树脂基、金属基、陶瓷基和碳-碳复合材料。在国防军工中主要运用于飞机机身结构件。目前最先进的战机上复合材料用量已经达到40%,在空客最近推出的A350飞机上复合材料用量更是高达52%。预计未来5年军用航空市场需求量达到10.2万吨,市场空间超过200亿元;未来20年民用航空市场需求量达到35.4万吨,市场空间超过700亿元。
钛合金:钛合金具有较高的抗拉强度,较低的密度,优良的抗腐蚀性能,在300〜550℃温度下有一定的高温持久强度同时具有很好的低温冲击韧性,是一种理想的轻质结构材料。钬合金在航空工业中的应用主要是制作飞机的机身结构件、起落架、支撑梁、发动机压气机盘。它在F-22飞机上的用量占结构重量的41%,在波音787上用量达到15%, 在A320上的V2500发动机上的用量达到31%。预计未来5年我国军用航空领域的钛合金市场规模为142亿元,未来20年民用航空领域的钛合金市场为265.5亿元。
超材料:超材料是一种由材料构成的“材料”。其中,介于宏观和微观之间的结构是超材料的基本组成单元。超材料技术是一种材料逆向设计技术,具有超越自然界材料电磁响应极限的特性。目前主要的国防应用集中在超材料隐身技术、超材料特种天线和超材料雷达罩等领域。未来20年超材料在国防军工的市场空间巨大,仅军用飞机隐身材料应用就超过1,000亿,军舰应用市场也超过600亿。
超高强度钢:超高强度钢是屈服强度和抗拉强度分别超过1,200兆帕和1,400兆帕的钢, 它是为了满足飞机结构对强度的高要求而研发的。超高强度钢大量用于制造火箭发动器 压容器和一些常规武器。由于钛合金和复合材料在飞机上应用逐渐广泛,钢在飞机上用量有所减少,但是飞机上的关键承力构件仍采用超高强度钢。目前,在国际上有代表性的低合金超高强度钢300M,是典型的飞机起落架用钢。此外,低合金超高强度钢D6AC是典型的固体火箭发动机壳体材料。超高强度钢在不断提高韧性和抗应力腐蚀能力,未来会有更广泛的应用。预计2020年超高强度钢年市场规模近10亿。
高温合金——航空发动机关键材料
高温合金是在600℃以上的高温及一定及一定应力作用下长期工作的一类金属。高温合金区别于传统金属、合金的特点在于:在高温工作环境下合金具有较高的强度,良好的抗氧化和抗热腐蚀性能,良好的疲劳性能、断裂韧性,并在各种温度下保持良好的组织稳定性和使用可靠性等综合性能,在西方也称之为超合金(Superalloys)。
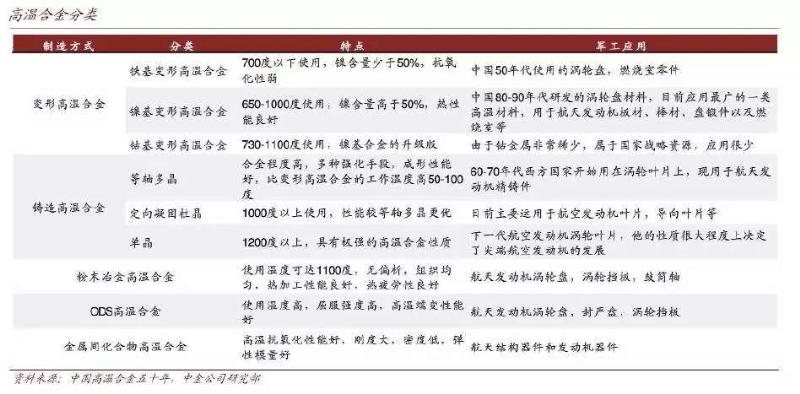
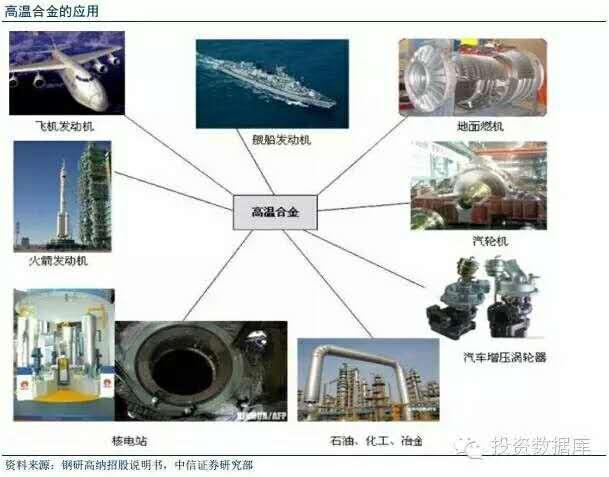
涡轮盘是几个部件中质量最大的,其工作温度并不是特别高,但是要承受各种复杂 应力,所以它的主要材料是变形高温合金;
燃烧室是将燃油的化学能转化为热能的场所,需要合金材料在800度以上的环境中 工作,所受的机械力较小热应力较大,目前主要材料为变形高温合金,但是随着发动机性能提升,变形高温合金已经达到其极限,现在开始尝试新型高温合金;
导向叶片是调整燃烧室出来的燃气的流动方向的部件,是受热冲击最大的零件之一, 需要足够的持久强度及良好的热疲劳能力,主要制造材料是铸造高温合金;
涡轮叶片是航空发动机上最关键的构件,因为涡轮前的燃气温度直接决定了发动机 的推重比,所以涡轮叶片材料的性能直接决定了发动机的性能,其工作环境最为恶劣,故采用最为先进的单晶合金。
综合来看,变形高温合金的耐热性能已经可以满足大部分的结构材料,只有部分核心零件比如涡轮叶片,这种工作环境极恶劣的零件需要铸造高温 合金或其他新型合金。由于变形合金的技术门槛较低,工艺相对简单,目前变形高温合金的需求量远大于铸造高温合金和其他类型合金。
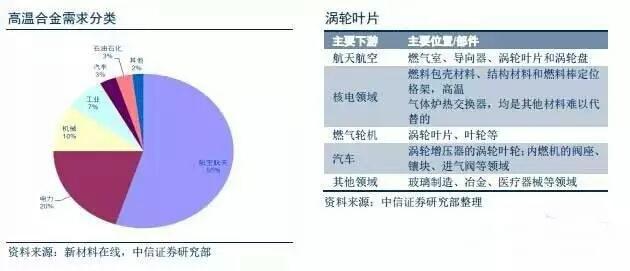
航空发动机
航空发动机被称为“工业之花”,是航空工业中技术含量最高、难度最大的部件之一。作为飞机动力装置的航空发动机,特别重要的是金属结构材料要具备轻质、高强、高韧、耐高温、抗氧化、耐腐蚀等性能,这几乎是结构材料中最高的性能要求。
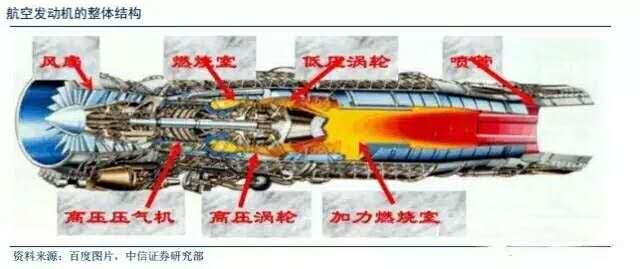
在现代先进的航空发动机中,高温合金材料用量占发动机总量的40%-60%。在航空发动机上,高温合金主要用于燃烧室、导向叶片、涡轮叶片和涡轮盘四大热段零部件;此外,还用于机匣、环件、加力燃烧室和尾喷口等部件。
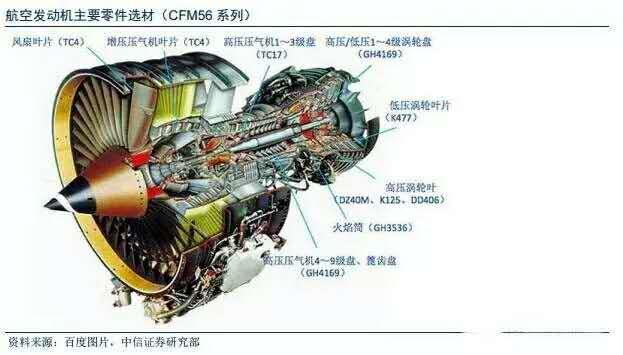
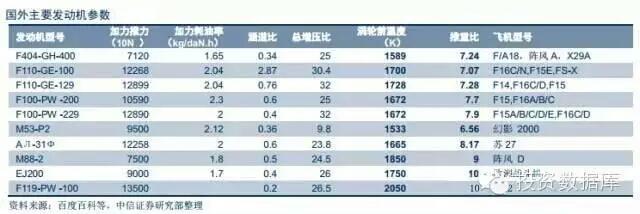
燃烧室的功用是把燃油的化学能释放变为热能,是动力机械能源的发源地。燃烧室内产生的燃气温度在1500~2000℃之间。其余的压缩空气在燃烧室周围流动,穿过室壁的槽孔使室壁保持冷却。燃烧筒合金材料承受温度可达800~900℃以上,局部可达1100℃。
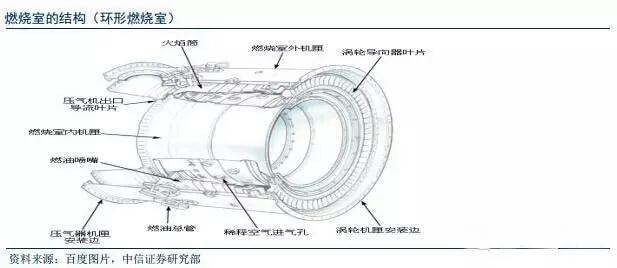
导向叶片
导向叶片是调整从燃烧室出来的燃气流动方向的部件,是航空发动机上受热冲击最大的零件之一。一般来讲,导向叶片的温度比同样条件下的涡轮叶片温度高约100℃,但叶片承受的应力比较低。
在熔模精铸技术突破后,铸造高温合金成为了导向叶片的主要制造材料。近年来,由于定向凝固工艺的发展,用定向合金制造导向叶片的工艺也在试制中;此外,FWS10发动机涡轮导向器后篦齿环制造采用了氧化物弥散强化高温合金。
涡轮盘
涡轮盘在四大热端部件中所占质量最大。涡轮盘工作时,轮缘温度达550-750℃,而轮心温度只有300℃左右,整个部件的温差大;转动时承受重大的离心力;启动和停车过程中承受大应力低疲劳周期。用于涡轮盘制造的主要材料是变型高温合金,其中G4169合金是用量最大、应用范围最广的一个主要品种。近年来,随着航空发动机性能不断提高,对涡轮盘要求也越来越高,粉末涡轮盘组织均匀、晶粒细小、强度高、塑性好等优点使其成为航空发动机上理想的涡轮盘合金,但我国工艺生产的粉末涡轮盘夹杂物较多,正在进一步研制中。
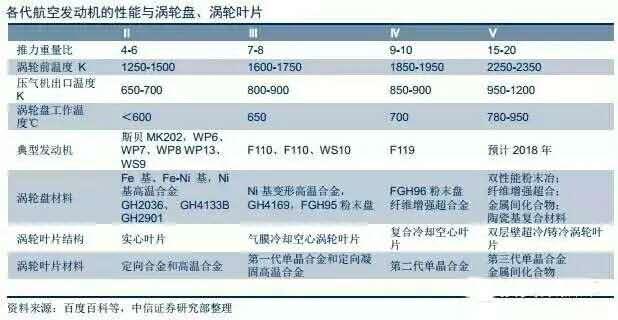
涡轮叶片是航空发动机上最关键的构件,涡轮叶片的工作环境最恶劣,涡轮叶片在承受高温同时要承受很大的离心应力、振动应力、热应力等。
用于涡轮叶片制造的主材材料是铸造高温合金。近三十多年来铸造工艺的发展,普通精铸、定向和单晶铸造叶片合金得到了广泛应用。单晶合金在国际上得到了快速发展,已经发展了五代单晶合金,成为高性能现金航空发动机高温涡轮工作叶片的主要材料;我国在20世纪80年代开始单晶合金研制,根据专著《中国高温合金50年》(师昌绪),第二代单晶合金已经在先进发动机中进行使用。
航天发动机
航天发动机中的特殊工作环境要求使其使用材料必须受高温、高压、高的温度梯度变化、高动态载荷和特殊戒指的考验,因此对材料的综合性能和加工性能提出了很高的要求。高温合金材料已经占据了航天发动机相当大的比重,在发动机中的应用比比例接近总重量的一半,高温合金材料技术的发展直接影响航天发动机研制水平。
航天发动机用高温合金原则上都可以采用航空发动机用高温合金,但航天发动机材料除了承受高温冲击外,还有低温(-100℃以下)环境要求。由于高温合金精密铸造工艺限制,过去形状极其复杂的结构件在航天发动机上一直没有真正加以应用。随着工艺的进步,航天发动机上的许多关键热部件都采用了无余量整体精密铸造高温合金精铸件,简化了发动机结构,降低发动机重量,减少了焊接部分,缩短研制和生产周期,降低研制和生产成本,提高发动机可靠性。随着航天发动机技术的进步,航天发动机用高温合金逐渐呈现出复杂化、薄壁化、复合化、多位一体、无余量的趋势。典型的有涡轮转子、导向器、泵壳体等。
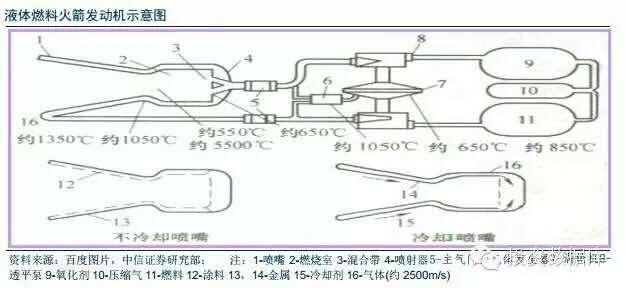
民用工业高温合金的应用
随着工业化的推进,工业向高端、大型化发展,高温合金在民用工业中的需求也日益增长。高温合金合金也是舰船、火车、汽车涡轮增压器叶片及各类工业燃机叶片的优选材料;铁路运输的高速化、造船业的高品质要求(特别是出口造船)、舰艇动力的高效要求、工业燃机应用的高速发展等急需高性能的高温合金母合金。目前,国内民用工业高温合金占高温合金总需求的20%,而美国50%的高温合金应用于民用工业领域。
燃气轮机
燃气轮机是高温合金的另一个主要用途。燃气轮机装置是一种以空气及燃气为介质的旋转式热力发动机,它的结构与飞机喷气式发动机一致,也类似蒸汽轮机。燃气轮机的基本原理与蒸汽轮机很相似,不同处在于工质不是蒸汽而是燃料燃烧后的烟气。燃气轮机属于内燃机,所以也叫内燃气轮机。构造有四大部分:空气压缩机,燃烧室,叶轮系统及回热装置。
燃气轮机的需求增长迅速,除用于发电外,还用于舰船动力、天然气疏松的加气站等。与航空用高温合金叶片相比,燃气轮机用高温合金的使用寿命长(10万小时),耐热腐蚀、尺寸大,质量要求很高。
汽车废气涡轮增加器
汽车废气增压器涡轮也是高温合金材料的重要应用领域。目前,我国涡轮增压器生产厂家所采用的涡轮叶轮多为镍基高温合金涡轮叶轮,它和涡轮轴、压气机叶轮共同组成一个转子。此外内燃机的阀座、镶块、进气阀、密封弹簧、火花塞、螺栓等都可以采用铁基或镍基高温合金。
涡轮增压系统对燃油效率和性能提升均有明显效果。涡轮增压是利用发动机排出的废气的能量来推动涡轮室内的涡轮,涡轮又带动同轴的叶轮,叶轮压送由空气滤清器管道送来的空气,使之增压进入气缸。当发动机转速增快,废气排出速度与涡轮转速也同步增快,叶轮就压缩更多的空气进入气缸,空气的压力和密度增大可以燃烧更多的燃料,相应增加燃料量就可以增加发动机的输出功率。一般而言,加装废气涡轮增压器后的发动机功率及扭矩要增大20%—60%。
核电与其它领域的高温合金应用
核电工业使用的高温合金包括:燃料元件包壳材料、结构材料和燃料棒定位格架,高温气体炉热交换器等,均是其他材料难以代替的。例如,燃料元件包壳管的管壁在工作时需承受600-800℃的高温,需要较高的蠕变强度,因此大量采用高温合金材料。
高温合金材料在玻璃制造、冶金、医疗器械等领域也有着广泛的用途。在玻璃工业中应用的高温合金零件多达十几种,如:生产玻璃棉的离心头和火焰喷吹坩埚,平板玻璃生产用的转向辊拉管机大轴、端头和通气管、玻璃炉窑的料道、闸板、马弗套、料碗和电极棒等。冶金工业的轧钢厂加热炉的垫块、线材连轧导板和高温炉热电偶保护套管等。医疗器械领域的人工关节等。
高端高温合金被国外垄断
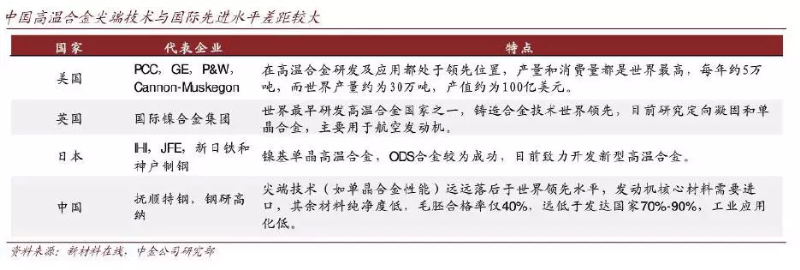
国内高温合金市场较为分散
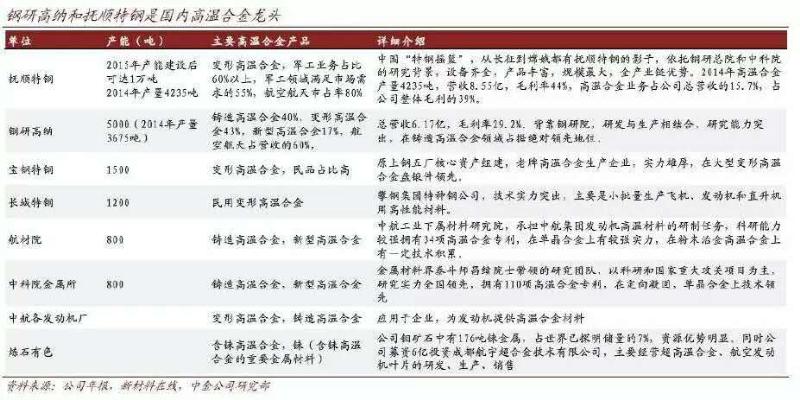
钢研高纳和抚顺特钢是国内高温合金龙头。在国内,目前消耗量最大的变形高温合金主 要由抚顺特钢、钢研高纳、宝钢特钢、长城特钢等企业生产,此类企业善于生产大批量、通用型、结构较为简单的产品。铸造高温合金主要是由钢研高纳、中科院金属所和航材 院以及各发动机厂专属精铸件厂生产,前三者主要是承接发动机厂对外委托的精铸件业 务。抚顺特钢和钢研高纳是两个方向的龙头企业,两者在变形高温合金业务上有一定竞 争,但总体发展方向不同。抚顺特钢以提高产量降低成本为发展方向;钢研高纳走研发 加产业化道路,产品更高端更具针对性。
高温合金的市场空间测算
根据测算,我们认为到2020年,国内高温合金需求约为39275吨,对应市场空间90.5亿元。
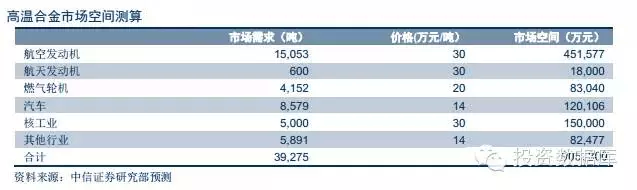
假设1:在航空发动机中高温合金占总重量的40%-60%,在先进发动机中这一比例超过50%甚至更多。我们判断,随着航空工业的继续发展和高温合金材料科技的进步,这一比例还将继续提升。我们假设高温合金占军用航空发动机重量的60%,占民用航空发动机和其他军机重量的40%。
假设2:通过与已有国内外相似型号飞机发动机规格对比,我们假设军用战斗机发动机重量约1.7吨,军用运输机、民用大飞机发动机重量约4吨,其他飞机航空发动机重量约1吨。
假设3:高温合金的材料性能、加工难度要高于普通合金和钢材,其材料成型率远低于一般特钢。我们估计,1)在铸造和轧制过程中材料成型率70-80%左右;2)母合金进行加工时,废品率80%左右,全流程材料利用率15%-20%,我们假设高温合金全流程材料利用率为20%。
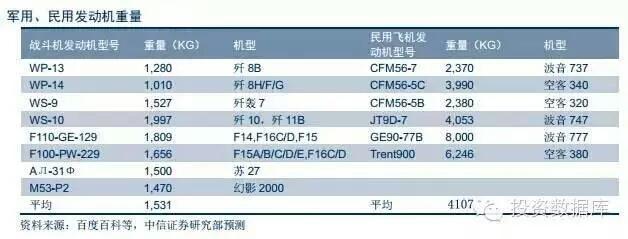
根据测算,未来20年我国军用航空发动机高温合金需求为17.75万吨,民用大中型飞机发动机高温合金需求为7.36万吨。此外,低空开放将有望打开我国通用航空发展的瓶颈,未来20年通用航空保有量超过20000架,以平均1台发动机测算,通用航空发动机高温合金需求为5万吨。
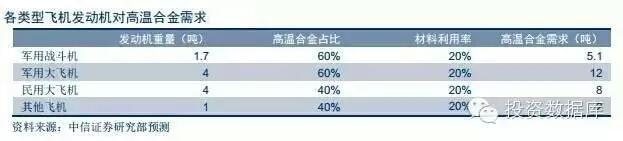
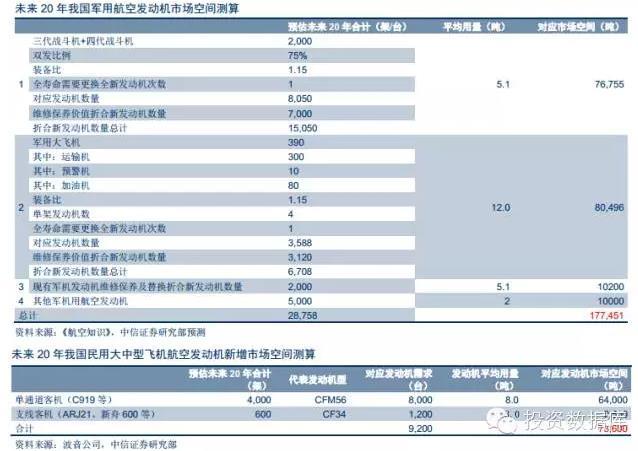
军事应用占世界船用燃气轮机市场绝大多数份额。在军用领域,有75%以上的海军主力舰艇采用燃机动力;在民用市场,燃机主要应用于高速客船中。
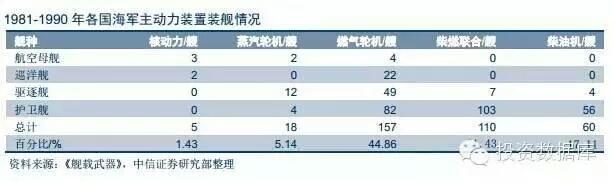
随着中国多型船用燃机相继研制成功,中短期内燃机普及有望提速。我们认为,燃机普及将以30MW级船用燃机为核心,辅以4MW级小功率船用燃机。其中,30MW级燃机主要用于大型的驱逐舰、护卫舰等;4MW级燃机主要用于气垫登陆艇和导弹快艇。
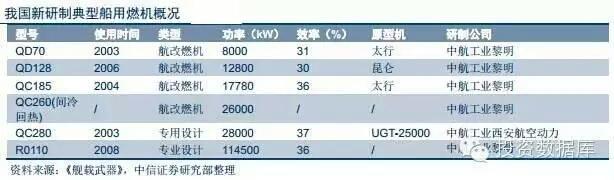
未来15年,我们认为海军将形成3大近海防御舰队+若干支航母编队+若干只两栖攻击/登陆编队为主体的作战体系。考虑到燃机应用情况,常规/核动力航母、两栖攻击/船坞登陆舰将其作为主要动力源的可能性较小,应用燃机的新型舰艇很可能主要配备在航母编队和两栖攻击/登陆编队中,且以驱逐舰和护卫舰为主,近海防御舰队则仅配备新型隐身导弹艇。
按照未来15年将建设5个航母编队(2常+3核)、3个两栖攻击/登陆编队和3个近海防御舰队规模的假设,再考虑到燃机的更新与维护,我们估算未来15年30MW级燃机需求600台,4MW级燃机需求1476台。通过测算,未来15年燃气轮机高温合金需求达6.23万吨,平均每年4152吨。
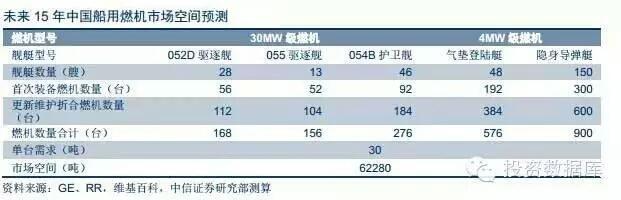
复合材料是由2种或2种以上的材料经过复合工艺制备的多相材料,各种材料在性能上互相影响,产生协同效应,使复合材料的综合性能优于原组分材料而满足各种不同的要求。复合材料由连续相的基体和被基体包容的分散相增强体组成。
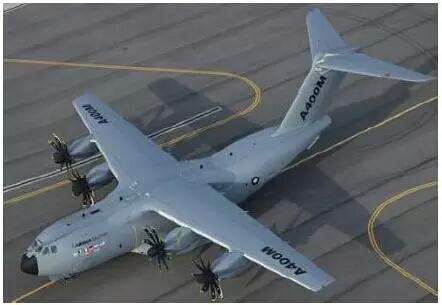
先进复合材料是比通用材料有更高综合性能的新型材料,其最重要的特点便是轻质高能,而这正是军事工业对武器装备的设计理念和奋斗目标,因此它在军事工业的发展中起着举足轻重的作用。
玻璃纤维复合材料
玻纤增强树脂基复合材料是最早应用于军事领域的复合材料之一。目前用于高性能复合材料的玻璃纤维主要有高强度玻璃纤维、石英玻璃纤维和高硅氧玻璃纤维等,其中后2种玻璃纤维属于耐高温的玻璃纤维,是较为理想的耐热防火材料,用其增强的复合材料部件大量应用于火箭、导弹的防热材料,另外玻璃纤维价格便宜,其高性价比受到应用领域的青睐。
在轻型装甲车中,玻璃纤维复合材料的应用几乎涉及装甲车辆的各个部位,如侧裙板、翼子板、各种油箱盖板、复合装甲板等,比具有同等功能的金属材料大大减轻了车辆的重量。
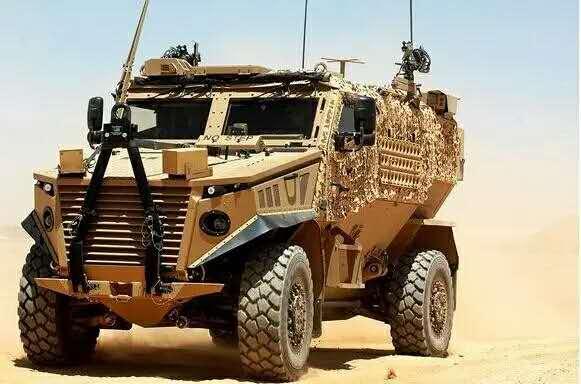
碳纤维复合材料
碳纤维是一种直径范围在6~8μm以内的连续细丝材料,碳纤维复合材料是用碳纤维和高性能的树脂基体复合而成的先进树脂基复合材料,是目前用得最多、最重要的一种结构复合材料。另外,对于军用飞机可以屏蔽或衰减雷达波与红外特征,提高自身生存和空防能力,在实现战机轻量化、快速反应、精确打击等方面起着巨大作用,因此,碳纤维复合材料也是目前在军用战机领域用得最多的一种复合材料,例如,在A400M军用战机上,复合材料占结构重量的比例达35%~40%,特别是机翼,碳纤维复合材料占机翼结构重量比例高达85%。图是A400M碳纤维复合材料战机。
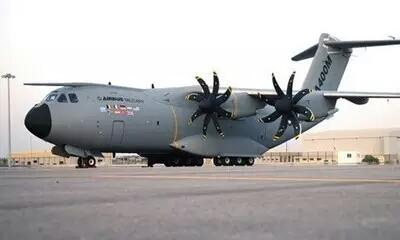
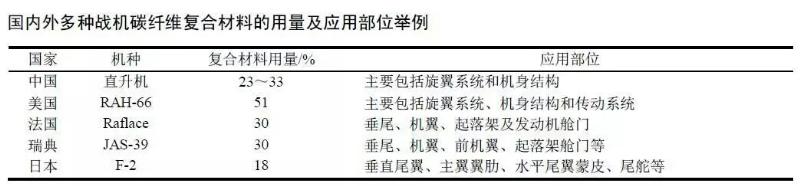
芳纶纤维是一种高强度、高模量、低密度、耐高温、耐腐蚀和高耐磨的有机合成纤维,由于其综合性能优异,其复合材料也具有优异的性能,因而芳纶复合材料在军事领域受到国内外的高度重视和广泛应用。
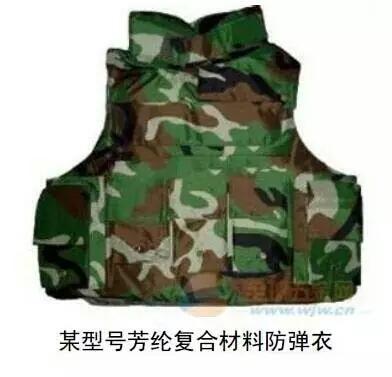
芳纶复合材料在军事上的另一个重要应用便是用于人体防护,主要是指防弹衣、防刺服、防割手套和防弹头盔等。图是芳纶复合材料某防弹衣。
聚乙烯复合材料
聚乙烯复合材料最突出的特点便是轻质高能。相比于玻璃纤维、碳纤维和芳纶纤维,聚乙烯纤维质量最轻,密度约为0.97g·cm-3,而聚乙烯纤维复合材料的比冲击总吸收能量分别是碳纤维、芳纶和E玻璃纤维的1.8、2.6和3倍,其防弹能力比芳纶装甲结构的防高弹能力高2.6倍。因此,聚乙烯复合材料是航空航天、防弹防刺等国防领域追求轻质高能的理想材料。
在军事上,聚乙烯复合材料主要用于装甲的壳体、雷达防护外壳、头盔、坦克的防碎片内衬、防弹衣等。我国聚乙烯复合材料的起步较晚,但发展迅速。目前,上海斯瑞有限公司自主研发的由SD301聚乙烯纤维复合材料模压的防弹插板、防弹衣、防刺服等,其防护性能高于世界先进水平,已经成功应用于多种装甲防护车辆及人体防护。聚乙烯复合材料在轻质高能方面的突出特性为其赢得了国内外的度重视和在军事领域的广泛应用,例如,英国T.B.A公司生产的防弹服和AIIiedIignaI公司的一种防护夹层由聚乙烯复合材料制得,另外,俄罗斯、日本的防弹、防刺产品也广泛采用了聚乙烯复合材料。
复合材料技术的民事应用
复合材料技术的发展发端于国防科技工业领域,经过多年发展,复合材料技术在国民经济各领域的应用不断扩大。复合材料产品不仅应用在军用方面,近年来种类繁多的民用复合材料产品大量涌现,复合材料与传统材料相比有很多优点,复合材料在航空、汽车、房屋补强、隧道工程以及大型储仓修补和加固等领域被广泛应用。特别是航空航天领域,成为全球复合材料市场中最大的单体市场,随着复合材料技术的进一步成熟,民用飞机的复合材料用量在大幅度提高,例如,波音公司的波音787飞机和空客公司的A350WXB飞机复合材料用量已达到甚至超过了50%。另外,在2010年航空业使用的2000多万公斤复合材料中碳纤维复合材料占37%,玻璃纤维复合材料占35%,其他复合材料占28%。
国外复合材料技术的应用比中国更早,对人们的日常生活覆盖得越更广,但其应用领域基本是相同的。基于复合材料具有轻质高能、耐磨、防腐等一系列共性,在民用工业中的应用大多数是相互交叉的,但根据复合材料各自增强材料的不同,其应用领域也有略微差别,图3为主要复合材料产品在民事领域的应用。表是以上4类复合材料的在民用工业中的主要应用领域。
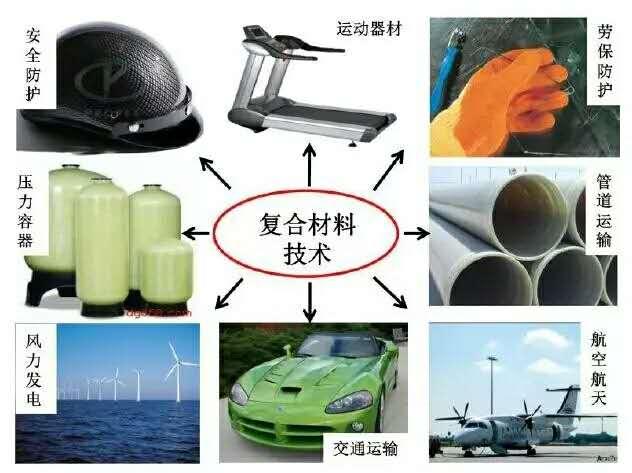
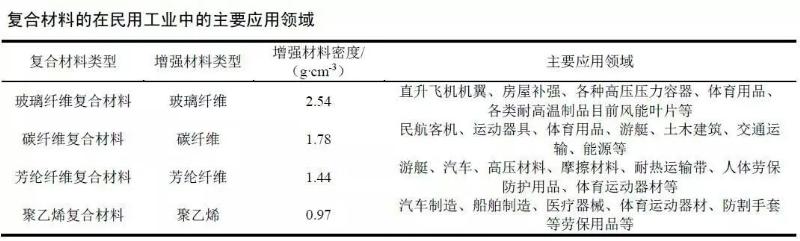
全球复合材料总产量已超过1000万吨,其中美国占据领先位置,占全球产量的28%。 据JEC预测,美国复合材料工业将保持5%的年增长,主要由航空、车辆及建筑三大领域驱动。
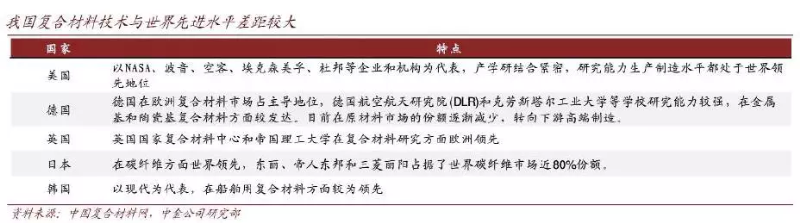
中国的复合材料技术与世界领先水平存在相当大的差距,特别是碳纤维方面,中国生产出来的碳纤维不均率高,毛丝多,力学性能不佳根本无法用来制造航天装备,比如广泛用于飞机机身的T800碳纤维,国外已经能够实现高性能化、低成本化和系列化,中国在2014年以前只能靠进口。在玻璃纤维方面我国与国际领先水平差距不大,但是玻璃纤维制作工艺简单,性能也远不如其他复合材料。
我国战机复合材料使用量大约占总重6~9%,主要用于机翼、平尾、前机身,直升机使用量占总重的25〜33%,主要用于机身和旋转机构件。
复合材料航空市场空间广阔 我国目前正不断加强对航空领域复合材料的重视,预计未来我国航空飞行器中复合材料 的使用量会进一步提高,我们假设中国飞机未来几年复合材料的使用比例达到美国90年代水平,航空用复合材料制造损耗率为75〜80%,由此我们估算2015〜2020年军用航空复合材料市场需求量为10.2万吨,市场空间超过20亿元;2015〜2033年民用航空复合材料市场需求量为35.4万吨,市场空间超过700亿元。
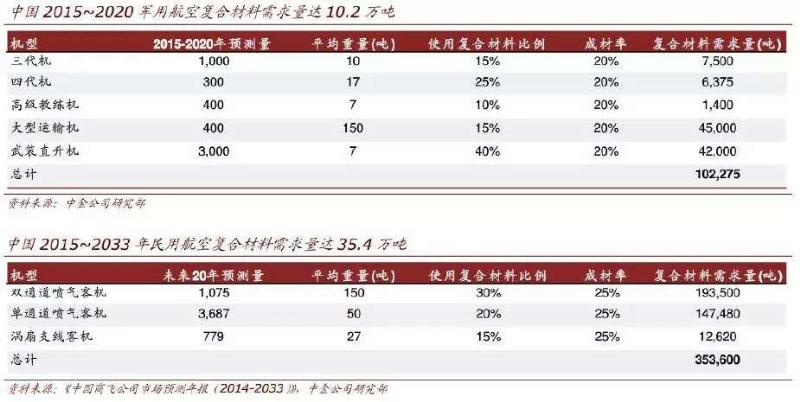